Write4U
Valued Senior Member
continued.......
Stretchable, Twisted Conductive Microtubules for Wearable Computing, Robotics, Electronics, and Healthcare
Thanh Nho Do & Yon Visell
Scientific Reports volume 7, Article number: 1753 (2017) Cite this article
Abstract
Fabrication process for the conductive microtubules. (a) Spin coat a thin layer of liquid polymer (here, Ecoflex 00-30) onto a silicon wafer, (b) rolling coat the carbon rod with the thin layer of liquid polymer, (c) heat with a hot plate, (d) peel off the hollow microtubule, (e) inject liquid metal (EGaIn) into the hollow microtubule using a needle and syringe, (f) insert electrodes into both ends of the microtubules and twist. Structure of the microtubules with (g) different numbers of turns per twisted pair, (h) woven electronic sensing fabric using twisted conductive microtubules. Detail: Cross-sectional SEM image of microtubule. Bar scale: 100 µm.
...more
https://www.nature.com/articles/s41598-017-01898-8
World of Carbon Nanotubes Stage Presentation and Posters
...much more
https://www.nisenet.org/catalog/programs/world_carbon_nanotubes
Stretchable, Twisted Conductive Microtubules for Wearable Computing, Robotics, Electronics, and Healthcare
Thanh Nho Do & Yon Visell
Scientific Reports volume 7, Article number: 1753 (2017) Cite this article
Abstract
Stretchable and flexible multifunctional electronic components, including sensors and actuators, have received increasing attention in robotics, electronics, wearable, and healthcare applications. Despite advances, it has remained challenging to design analogs of many electronic components to be highly stretchable, to be efficient to fabricate, and to provide control over electronic performance. Here, we describe highly elastic sensors and interconnects formed from thin, twisted conductive microtubules. These devices consist of twisted assemblies of thin, highly stretchable (>400%) elastomer tubules filled with liquid conductor (eutectic gallium indium, EGaIn), and fabricated using a simple roller coating process. As we demonstrate, these devices can operate as multimodal sensors for strain, rotation, contact force, or contact location. We also show that, through twisting, it is possible to control their mechanical performance and electronic sensitivity.
In extensive experiments, we have evaluated the capabilities of these devices, and have prototyped an array of applications in several domains of stretchable and wearable electronics. These devices provide a novel, low cost solution for high performance stretchable electronics with broad applications in industry, healthcare, and consumer electronics, to emerging product categories of high potential economic and societal significance.
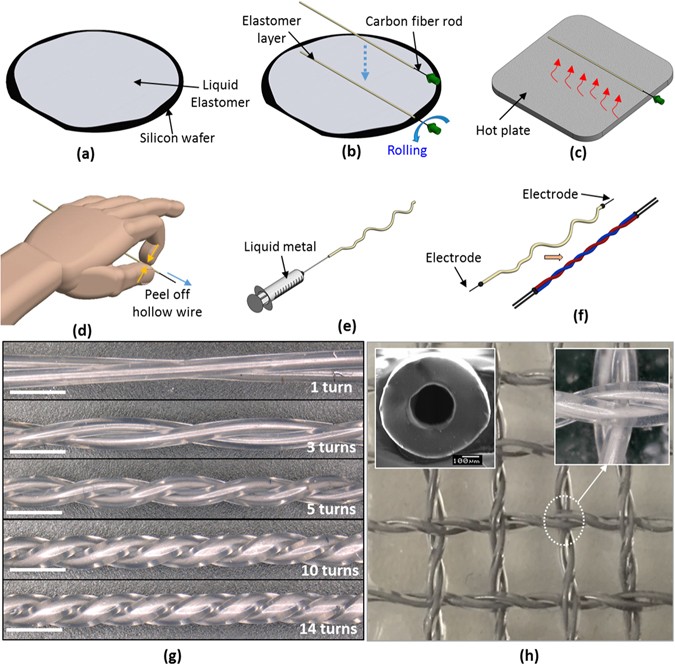
Fabrication process for the conductive microtubules. (a) Spin coat a thin layer of liquid polymer (here, Ecoflex 00-30) onto a silicon wafer, (b) rolling coat the carbon rod with the thin layer of liquid polymer, (c) heat with a hot plate, (d) peel off the hollow microtubule, (e) inject liquid metal (EGaIn) into the hollow microtubule using a needle and syringe, (f) insert electrodes into both ends of the microtubules and twist. Structure of the microtubules with (g) different numbers of turns per twisted pair, (h) woven electronic sensing fabric using twisted conductive microtubules. Detail: Cross-sectional SEM image of microtubule. Bar scale: 100 µm.
...more
https://www.nature.com/articles/s41598-017-01898-8
World of Carbon Nanotubes Stage Presentation and Posters
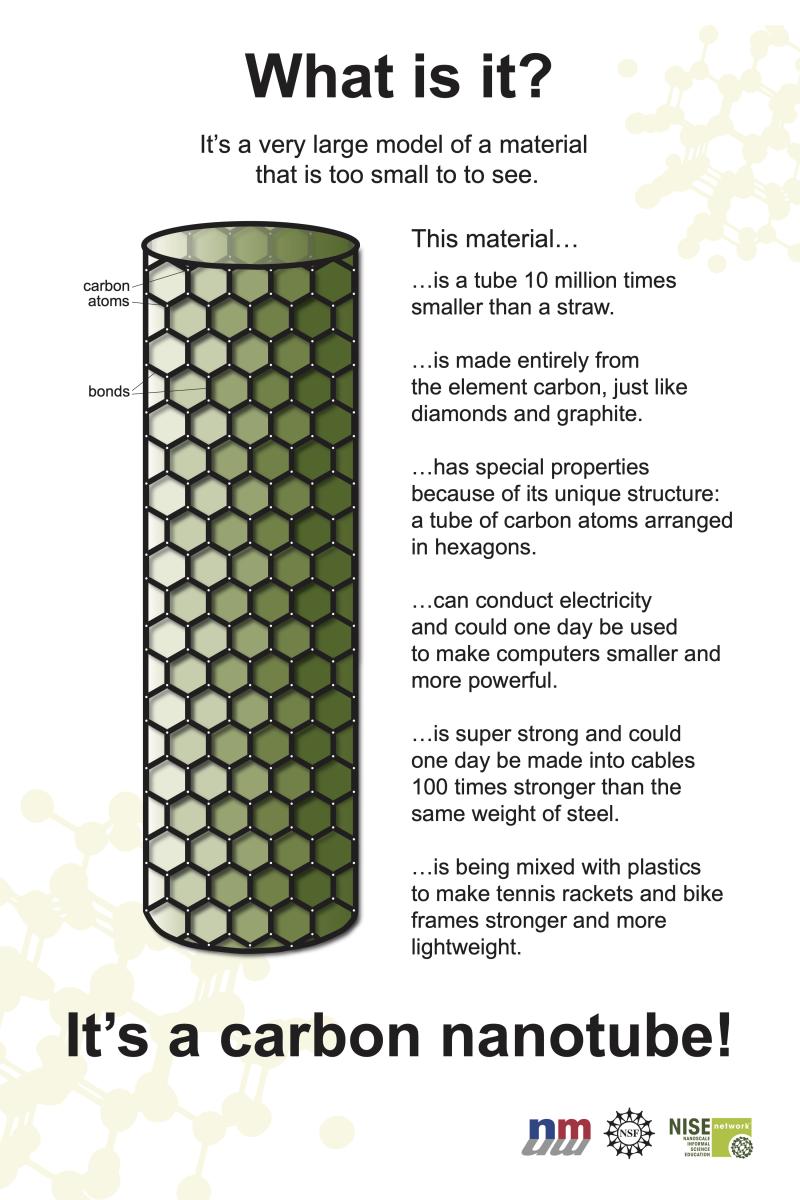
...much more
https://www.nisenet.org/catalog/programs/world_carbon_nanotubes